Understanding Spinning Wheel Double Drive Mechanics

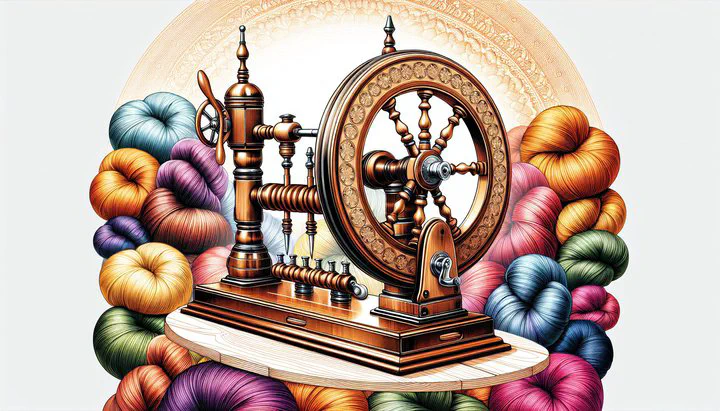
Mastering Spinning Wheel Double Drive Mechanics: A Beginner’s Guide
Have you ever wondered how crafters turn fluffy clouds of wool into beautiful yarn? It all starts with the magic of a spinning wheel! A spinning wheel is a fascinating tool used by crafters to spin fiber into yarn. It’s been around for centuries, and today, we’re going to explore how it works, especially focusing on the double drive mechanics.
At its core, a spinning wheel has a few basic parts that help it do its magic. There’s the wheel itself, which you turn by using a pedal or hand. This wheel is connected to a smaller spindle, which twists the fibers and turns them into yarn. But what really makes the spinning wheel special is how all these parts work together to spin the fiber smoothly.
One of the most interesting features of some spinning wheels is the double drive system. In a double drive, both the flyer and the spool are driven by the wheel. This setup gives you more control over the tension, making it easier to create even and smooth yarn. It’s a bit like having a car with a turbo engine—more power and precision! This method is favored by many experienced spinners because it offers a more consistent spin, which is especially helpful when working with different types of fiber.
Understanding these spinning wheel double drive mechanics can truly elevate your crafting skills. Whether you’re just starting out or you’ve been spinning for years, knowing how each part works will help you troubleshoot issues and improve your spinning. So, let’s dive into the mechanics and see how everything comes together to create the yarn you love!
Exploring the Flyer and Spool Relationship
When you’re using a spinning wheel with a double drive system, the flyer and spool relationship is key to turning your fiber into yarn. But what exactly do these parts do? Let’s break it down and see how they work together.
The flyer is like the hands that twist the fibers, while the spool is like the arms that hold your finished yarn. The flyer is a U-shaped piece that revolves around the spindle. It has hooks or loops that guide the yarn as it’s being spun, helping to twist it evenly. The spool, also called the bobbin, is where the spun yarn is collected. As the flyer spins, it winds the yarn onto the spool, which is crucial for creating a neat and tidy ball of yarn.
In a double drive setup, both the flyer and the spool are powered by the drive wheel. This means they spin at slightly different speeds, which allows for tension control. The flyer spins a bit faster than the spool, helping to add the necessary twist to the fiber before it’s wound up. This subtle difference is what allows the yarn to form correctly without breaking or becoming too loose.
But what happens if the alignment between the flyer and the spool is off? You might find that your yarn isn’t as smooth or even as you’d like. Common issues include uneven tension or yarn that won’t wind properly onto the spool. To fix these, ensure the drive bands are correctly positioned and that both the flyer and spool are clean and free from obstructions. Adjusting the tension can also help, making sure the yarn is winding on smoothly.
Understanding the flyer and spool relationship in your spinning wheel can make a big difference in your yarn quality. With these tips, you’ll be ready to tackle any challenges and keep your crafting projects on track. Now that we’ve explored these components, let’s move on to how the spindle fits into the picture.
The Role of the Spindle and Drive Wheel
In the world of spinning wheels, the spindle and the drive wheel are like the dynamic duo that keeps everything running smoothly. But why is the spindle screwed to the drive wheel, and how does this affect your spinning? Let’s unravel these mysteries!
Imagine the spindle and drive wheel as dance partners, moving together in perfect harmony to keep your yarn spinning just right. The spindle is a slender rod that plays a key role in twisting the fibers into yarn. It’s the part of the spinning wheel that transforms the fluffy wool into a tight, twisted strand. Picture the spindle as the heart of the spinning process—without it, there would be no yarn!
Now, you might be wondering why the spindle is screwed to the drive wheel. This design choice is crucial for maintaining a steady and reliable spin. When the spindle is securely attached to the drive wheel, it ensures that the twisting action is consistent. This connection allows the spindle to rotate at the same speed as the drive wheel, giving you the desired tension and twist in the yarn.
The setup where the spindle is screwed to the drive wheel enhances the efficiency and quality of your spinning. It provides stability, ensuring that the spindle doesn’t slip or wobble as you work. This means you can focus on your technique without worrying about mechanical hiccups. Plus, it helps maintain a smooth and even yarn, which is what every spinner aims for.
By understanding the role of the spindle and its connection to the drive wheel, you’ll gain more control over your spinning projects. This knowledge empowers you to troubleshoot any issues and fine-tune your setup for the best results. With the spindle and drive wheel working in harmony, you’ll be ready to create beautiful yarn with ease. Next, we’ll delve into the fascinating dynamics of why wool spins faster than the spool turns.
Why Wool Spins Faster than the Spool Turns
Have you ever noticed that when you’re spinning yarn, the wool seems to spin faster than the spool turns? This is a fascinating part of the spinning process, especially in a double drive system. Let’s uncover the mysteries behind this magic!
It’s like when you twirl a jump rope faster than your friend can catch it. In a double drive spinning wheel, both the flyer and spool are driven by the drive wheel, but they don’t spin at the same speed. The flyer rotates a bit faster than the spool, which is essential for adding the right amount of twist to the fiber. This difference in speed is what makes the wool spin faster than the spool turns. It’s all about the physics of tension and twist!
The flyer’s faster spin introduces more twists into the wool before it’s wound onto the spool. These twists are what hold the fibers together, turning them into strong and durable yarn. When the flyer spins quicker, it can twist the fibers rapidly while still allowing the spool to collect the yarn at a steady pace. This balance is what keeps your yarn from becoming too tight or too loose.
Several factors can influence how quickly the wool spins compared to the spool. The tension of the drive bands, the type of fiber you’re using, and even the humidity in the air can play a role. For the best results, you might need to adjust the tension or experiment with different fibers to see how they react.
To optimize this aspect of spinning, try adjusting your drive bands if you notice the yarn isn’t winding smoothly. If the wool is spinning too fast and breaking, increase the tension slightly. If it’s not twisting enough, decrease the tension. Understanding why wool spins faster than the spool turns allows you to control the quality of your yarn and ensure a successful spinning session.
With this knowledge, you can approach your spinning projects with confidence, knowing just how to tweak your setup for the perfect yarn. Next up, we’ll tackle some common issues that arise with double drive spinning wheels and how to troubleshoot them effectively.
Troubleshooting Common Double Drive Issues
Even the best spinners can run into problems with their double drive spinning wheels. It’s all part of the crafting journey! Let’s look at some common issues and how you can fix them, so your spinning stays smooth and enjoyable.
-
Uneven Tension: If your yarn keeps breaking or getting too loose, it could be because the drive bands are not properly adjusted. Check if they are slipping or if they’re too tight. You can fix this by adjusting the tension on the bands until you find the sweet spot where the yarn twists just right without breaking.
-
Yarn Not Winding Properly: This can happen if the flyer and spool relationship is off. Make sure that both parts are clean and free from lint or debris. Sometimes, the hooks on the flyer need a little adjustment, or the drive bands need repositioning. Gently cleaning and adjusting these components can often solve the winding problem.
-
Noisy or Wobbly Wheel: If your spinning wheel makes weird noises or feels wobbly, the connection where the spindle is screwed to the drive wheel might need attention. Ensure everything is tightly secured and check for any loose screws or parts. A little maintenance can go a long way in keeping things running smoothly. Lubricating the moving parts occasionally can also help reduce noise and friction.
To prevent future problems, regular maintenance is key. Clean your spinning wheel often, check the drive bands for wear and tear, and ensure all parts are in good working condition. Keeping a routine check will help you catch issues early and keep your spinning enjoyable and stress-free.
By following these troubleshooting tips, you’ll be able to handle any hiccups that come your way while using a double drive spinning wheel. With practice and care, you’ll master the art of spinning and create beautiful yarns for all your projects. Happy spinning!
In conclusion, the joy of creating with yarn is a rewarding experience that grows with every twist and turn of the wheel. Embrace the learning process, and don’t forget to share your projects with fellow crafters in online communities or on social media. Let’s keep the creativity spinning!